Industrial Hygiene Assessment Services
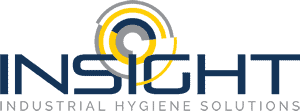
Insight Defined
in·sight (/inˌsīt/)
noun
the capacity to gain an accurate and deep intuitive understanding of a person or thing.
synonyms: perception, awareness, understanding, comprehension
The best means of determining workplace noise levels is through the use of personal dosimeters which are place on the shoulder of employees and worn for the full work shift. We can also perform sound level surveys using a handheld sound level meter (and can process the results into a color contour map overlaying your facility layout). The typical end product is a full report which documents observations, methodology, and results as they compared to applicable exposure limits.
A typical contaminant mapping job will consist of fixed area samples, multiple static background monitors, and a single portable monitor. We can complete most mapping activities in a single work shift. The end product will consist of a report documenting the workplace, multiple color contour maps of the measured concentrations overlaying the facility layout, and concentration graphs for the static monitors.
Typically real-time monitoring is conducted simultaneously with full-shift personal breathing samples. Often multiple monitors will be utilized, to determine both personal and background concentrations at each targeted workstation. The end product consists of a detailed report with real-time concentration graphs, statistical breakdowns of the gathered data, results tables, and a description of the work activities and methodologies used.